

- Sme tonearm placement on plinth full#
- Sme tonearm placement on plinth plus#
- Sme tonearm placement on plinth series#
Because of the peculiarities of the SME anti-skate, their arms are always at an angle to the chassis. The SME IV is now located at the rear left.
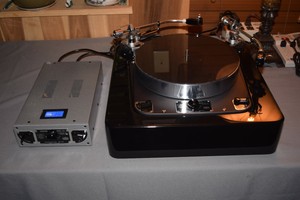
Because of the platter off-set, the V12 is mounted much closer to the chassis in this position with much less wasted plinth material, keeping the overall mass down. I chose to mount the SME V12 at the front right and rotate the plinth anti-clockwise by 90 degrees. This unnecessary expanse of plinth material increases the already high overall mass by upwards of 5 kg. The SP10R platter is off-centre to the square chassis, so when using a 12” tonearm in the standard position, there is a big space of plinth between the tonearm mount and the chassis. The Technics tonearms for the SL1000 are typically 10” and the chassis of the SP10R is just able to be used with a 9” tonearm like my SME IV in the standard position. Since I have a number of excellent tonearms and cartridges, I wanted to make maximum use of the SP10R by mounting multiple tonearms.
Sme tonearm placement on plinth full#
Of course, this is inconvenient if you want to change tonearms! My compromise is a substantial cast tonearm board similar to the bulk plinth material and rigidly connected around its full perimeter. As Yoda would say, “no tone-arm board is as good as no tone-arm board”. The chassis-plinth-tonearm connection is then as rigid as possible and better able to preserve the relative stylus-groove motion. My ideal tone-arm mounting is a drilled plinth top plate. I prefer a solid a mounting of the tone-arm+plinth+chassis. Secondly, the tonearm mounting boards are cantilevered from the edges of the SP10R chassis. Moreover, my experience is that extensional damping layers are outperformed by materials with high internal damping. Aluminium has a terrible damping factor compared to the best materials available. The bulk molding compound base is an extensional damping layer to control the aluminium top plate. The open base compromises torsional stiffness of the plinth, in my opinion. It is open at the bottom, with the SP10R secured by nine 5mm bolts around the perimeter.
Sme tonearm placement on plinth plus#
The SP10R plus arm boards drop into the SL1000R plinth, like a skirt.

There are a number of things I don’t like about the SL1000R plinth arrangement. Then the process of mold making, choice of mold inserts, extraction methods for the inserts, curing time, testing mold release compounds, repair of molding defects and prep for painting, base coats application, clear coats and buffing etc. Then the mixing and pouring technique took time to get right. Firstly the optimal formulation of resin+catalyst+bentonite. Using resin/bentonite required a quite lengthy learning process. Panzerholz is very expensive and hard to machine with typical DIY facilities, and was rejected. Panzerholz is the best but the resin/bentonite is close. He has compiled damping factor test results of standard samples of many candidate plinth materials. A while ago I settled on isophthalic polyester resin/bentonite compound cast into a mold, as promoted by a DIY Audio member Cat Squirrel. Applying damping layers to stiff substrates did not get the results I wanted. My finding is that starting with a material with superior internal damping works best. Over many years, I have tried many plinth materials and damping methods. A good plinth controls spurious motion due to counter torque by mass and damping.Ī properly damped plinth dissipates the reaction torque and main bearing noise, minimising the influence on the plinth/tonearm interface.
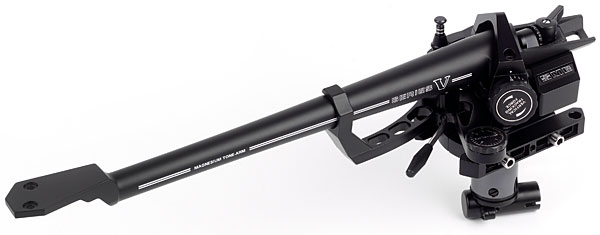
A counter torque is experienced by the mass of the chassis plus plinth. A direct-drive turntable like the SP10R has a constantly acting servomechanism that attempts to reduce speed fluctuations to an imperceptible level. For non-suspended high torque turntables such as the SP10 mkII and SP10R, attention to the fundamentals of mass, stiffness and damping of the plinth makes a noticeable difference to the sound quality. I have experienced first hand the effect that various plinth materials and construction methods can have on sound quality. I have used the mkII for two decades, in custom plinths of my own design and construction. The HFN review of the SL1000R raised concerns with the performance of the Technics plinth. Back in Sydney, I got down to the construction of a plinth for the mighty machine. (Thanks for the hospitality of my brief visit, Dave). I took possession of a Technics SP10R in August, courtesy of Dave Cawley.
Sme tonearm placement on plinth series#
I will break up my comments into a series of smaller posts.
